Flock Blog
Stay up to date with all things freight.
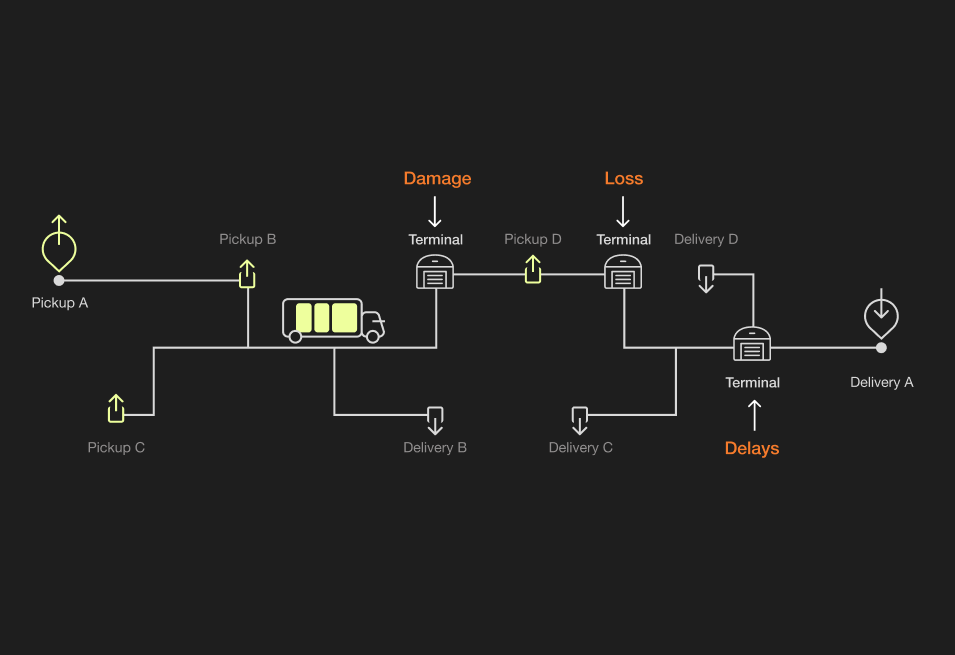
The Hidden Costs of Less Than Truckload Shipping
May 29, 2025
.png)
Why Shared Truckload scales better with Flock’s technology
April 30, 2025
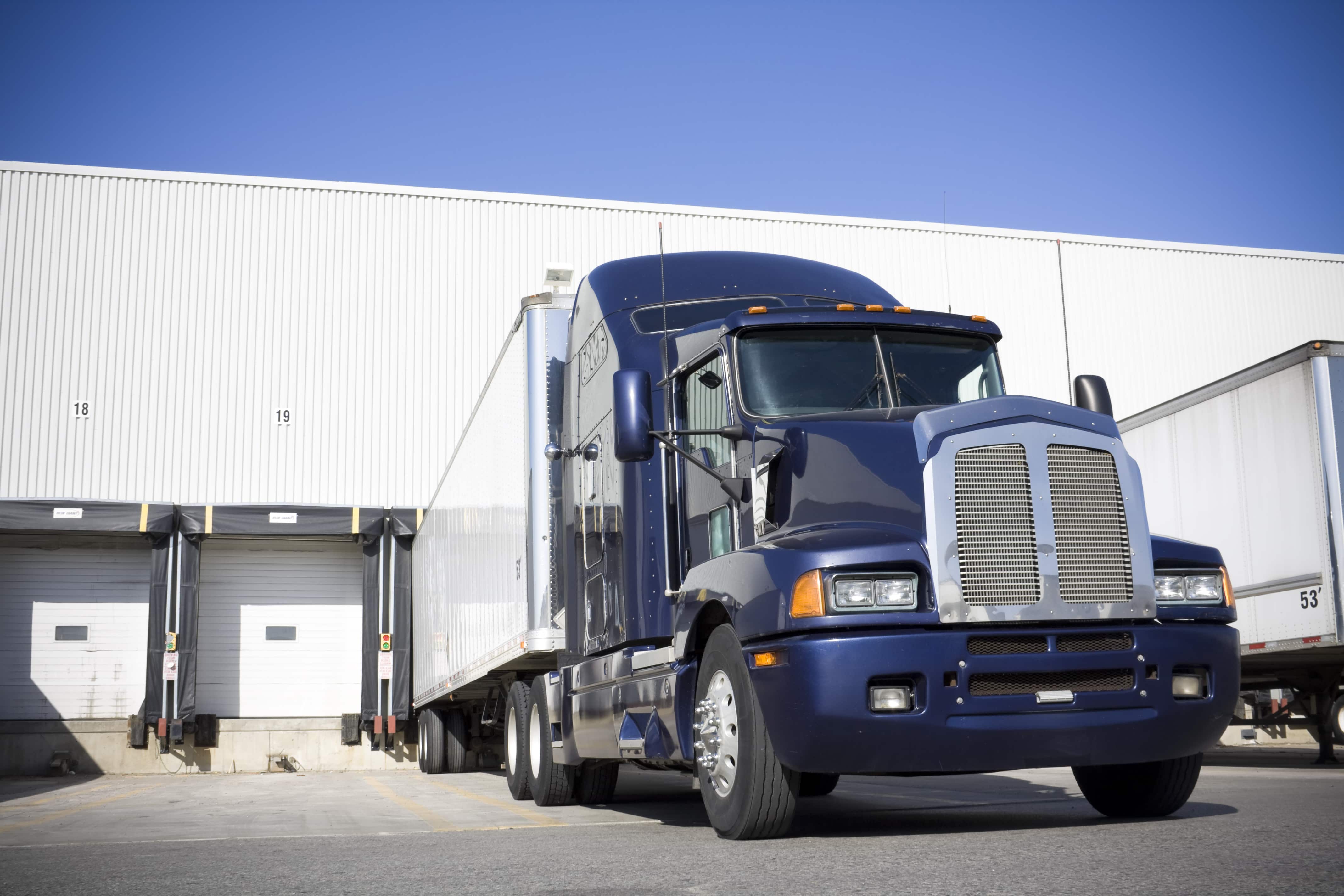
Freight Market Trends and Forecasts for Q2 2025
April 2, 2025
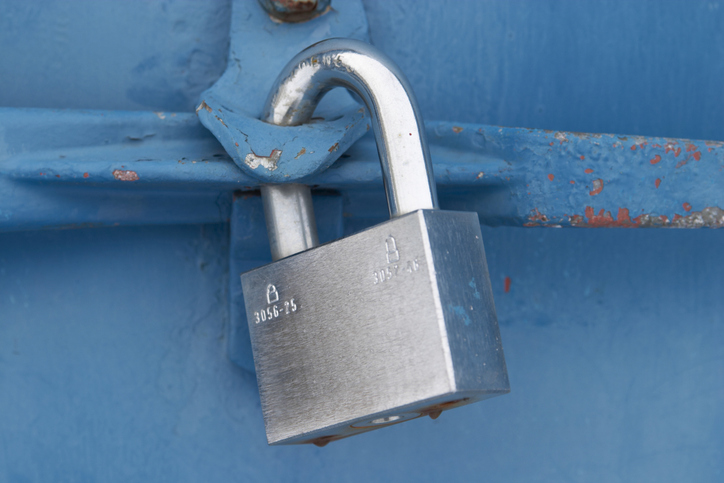
How to Avoid Cargo Fraud and Theft
December 18, 2024
.jpg)
How to Choose the Right Freight Carrier
October 23, 2024
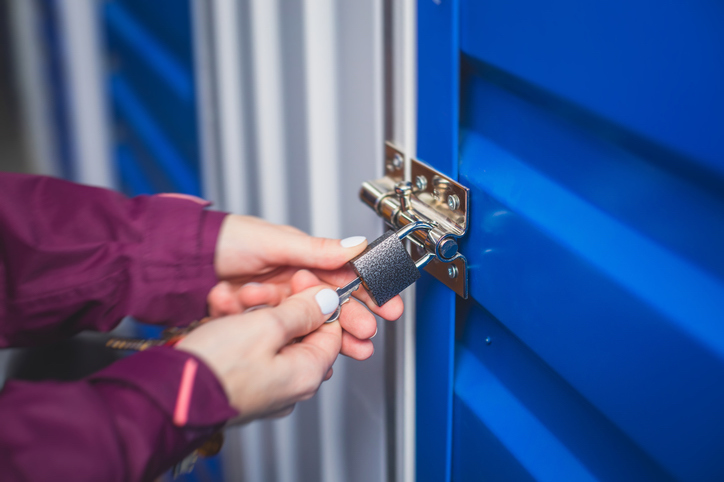
Understanding Freight Shipping Insurance: A Comprehensive Guide
October 23, 2024
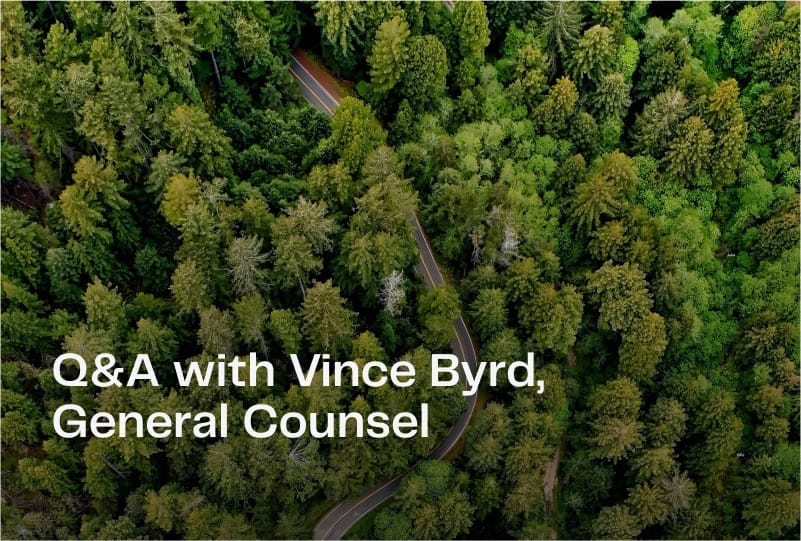
Flock Freight 2023 | Impact
January 24, 2024
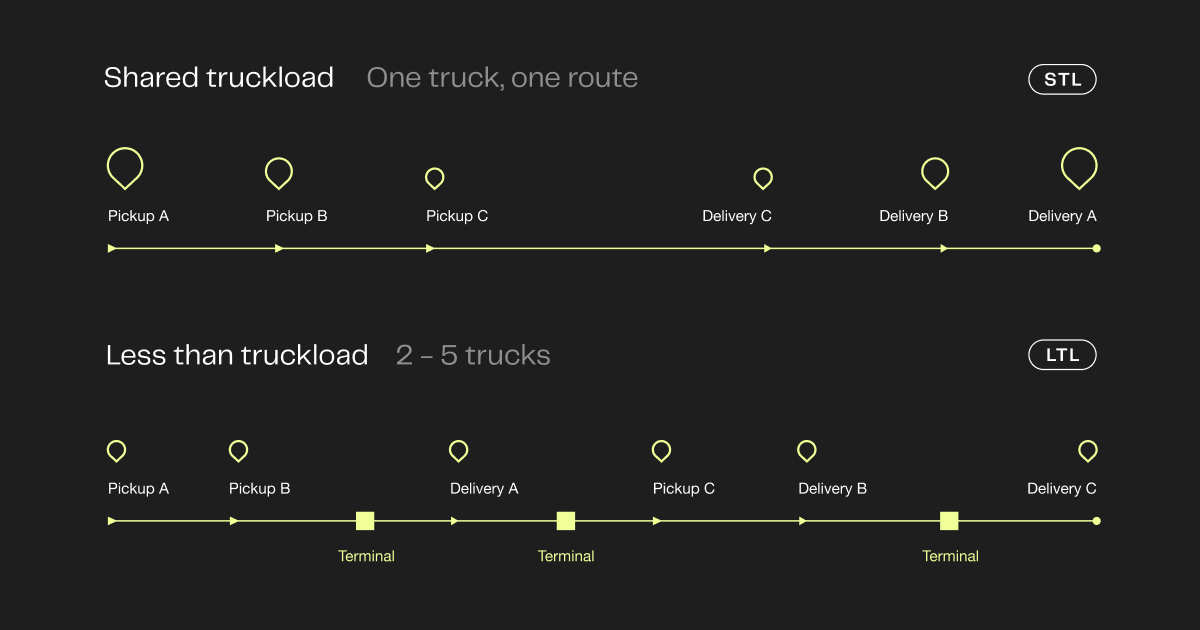
Volume LTL Shipping: What It Is & When To Use It.
October 26, 2023
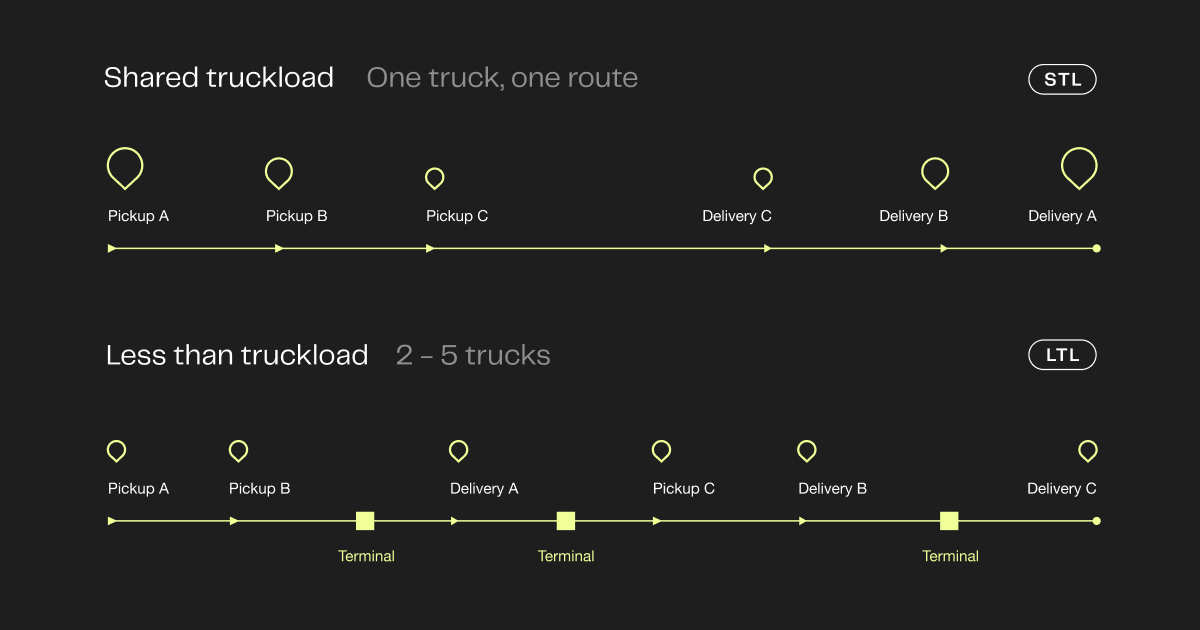
Shipping LTL vs STL
October 6, 2023
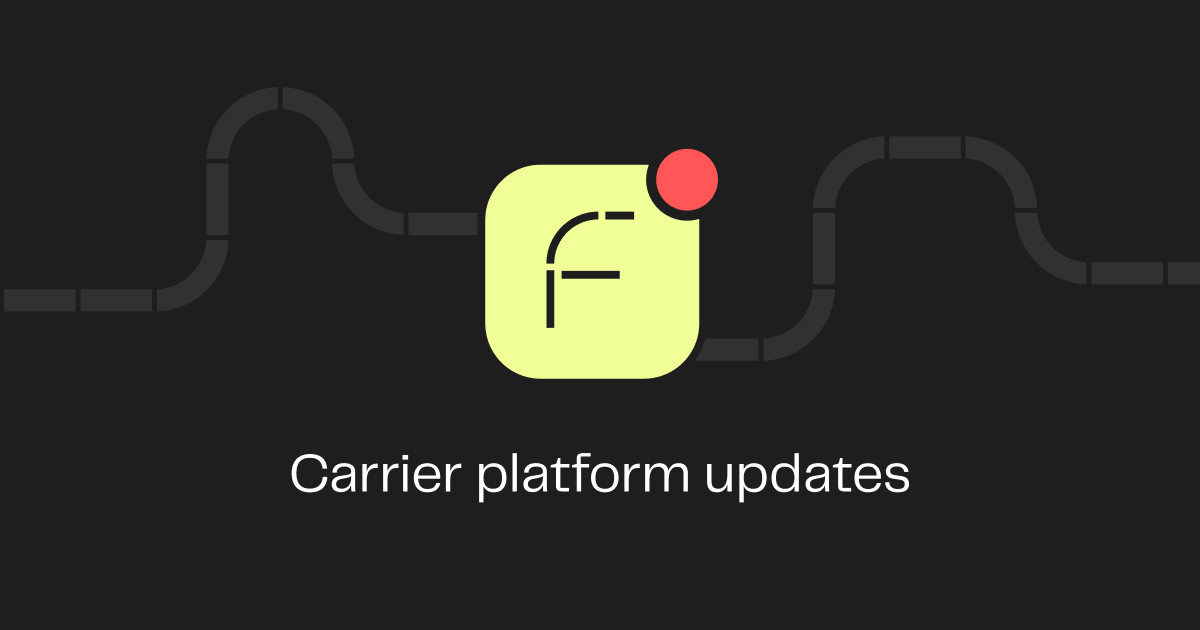
Platform Updates To Share Load Info & Streamline Dispatch
September 13, 2023
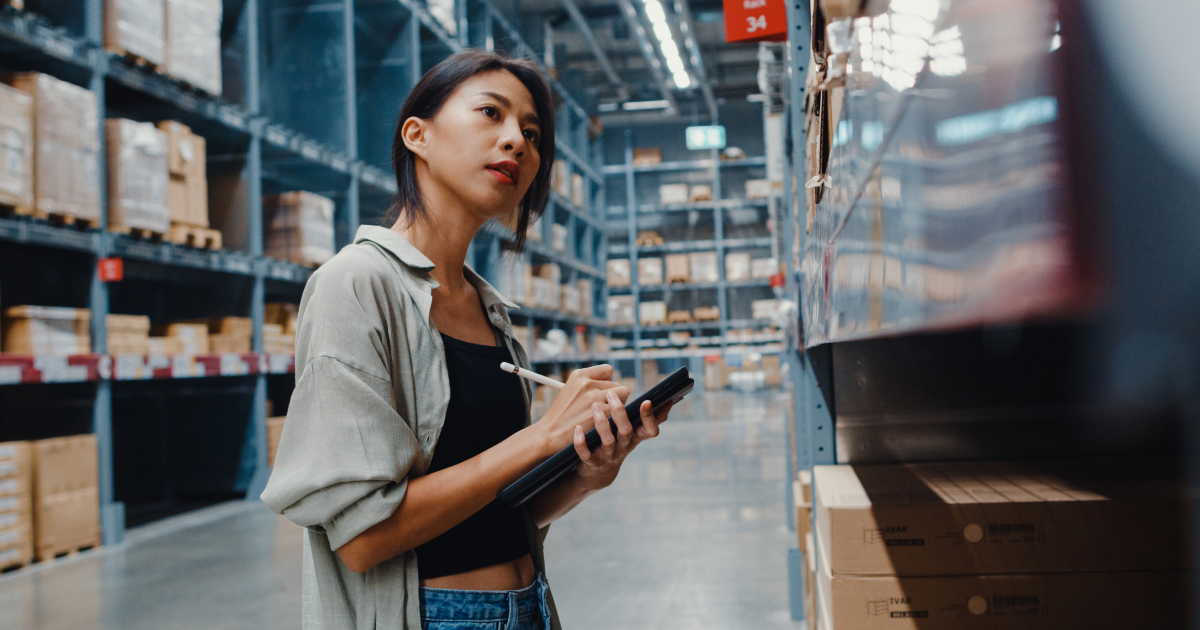
How to Calculate LTL Freight Quotes
August 25, 2023
.jpeg)
Shipping insurance for high-value electronics and tech
August 21, 2023