The Best Freight Shipping Mode for Furniture
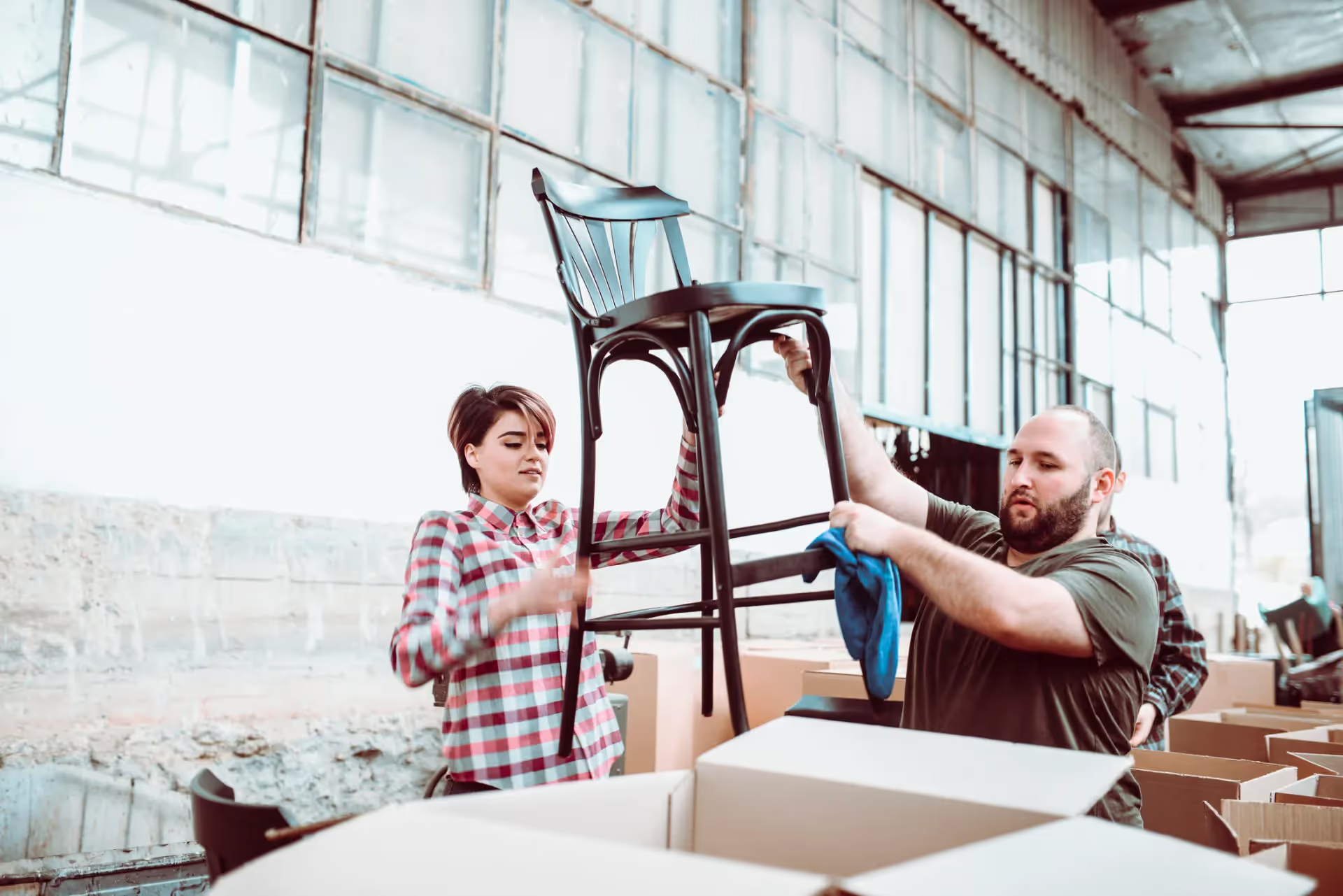
Plus, how one furniture shipper keeps cargo safe during cross-country transit...Table of contents
- Furniture shipping basics at a glance
- The cons of LTL and TL for furniture shipping
- Shared truckload has furniture shippers covered
- How FlockDirect keeps 100% of Grand Stands’ freight intact
- Out with the old, in with the new
2020 was the year the world started to look at furniture a bit differently. As companies transitioned to remote business models because of coronavirus, employees’ guest bedrooms, living rooms, and breakfast nooks alike became workspaces. Naturally, these traditionally non-work zones needed some sprucing-up to provide some semblance of office life. With storefronts out of commission and the general public in isolation, e-tailers were the logical choice for remote workers searching for home office furniture. How did new furniture orders arrive? Freight trucks.Fast-forward to 2021, when the COVID-19 vaccines have become widely available and desk workers have ventured back into offices. While some organizations have rethought the in-office model altogether, a sizable portion of them have been itching to resume work with staff under the same roof — at least part-time. The in-person proponents have another reality to consider, though: employee count might be much larger or smaller than it was pre-pandemic. To right-size office capacity, teams must space-plan (furniture-plan) for current headcount. How does furniture come and go? Freight trucks.To accommodate the needs of buyers, furniture makers must ship goods efficiently, which means booking reliable transportation.As a result of 2020’s fluctuating market, the furniture force has become as skilled at ironing out shipping wrinkles as linen and cotton ones.[sc name="anchtag" id="first" ]
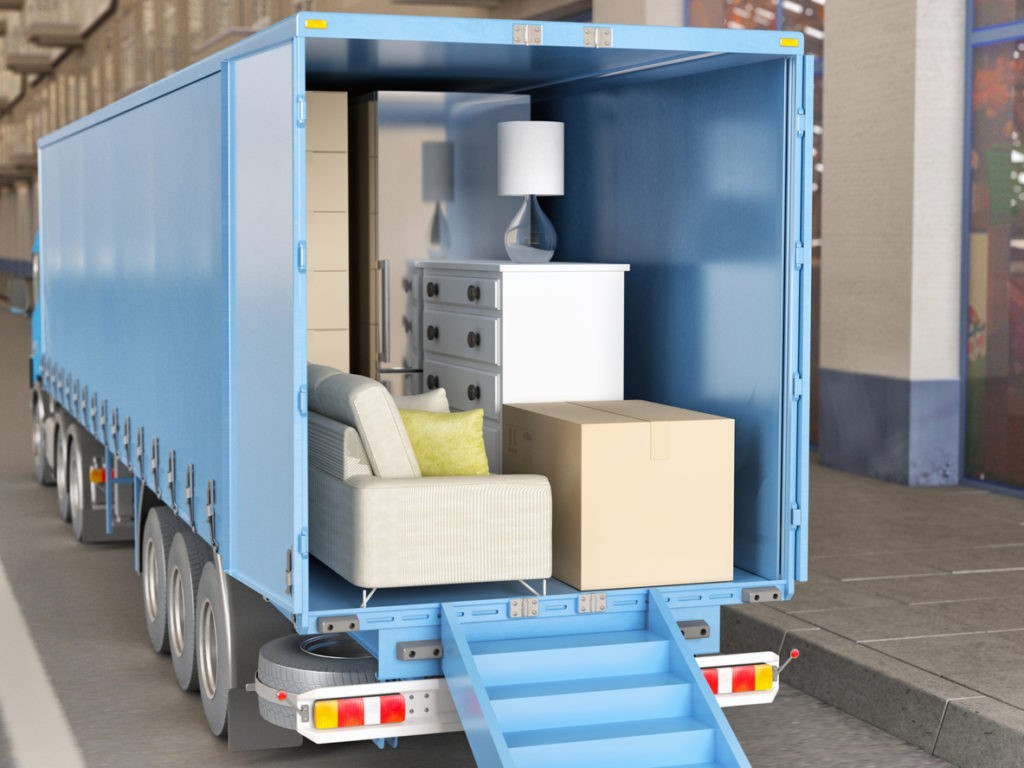
Furniture shipping basics at a glance
To meet demand, furniture shipping companies need to move products from one place to another — sometimes cross country — without damage or delay (and with finite budgets). This can be a tough goal to accomplish, especially considering furniture’s difficult dimensions and inconsistent shipping costs.The following characteristics make furniture hard to ship:
- Often takes up a lot of room.
- Relatively light per cubic foot (compared to other commodities).
- Sometimes palletized, other times floor-loaded.
- Relatively fragile items (compared to other commodities).
Those factors — combined with others — influence moving costs. Like other types of freight, furniture shipping costs vary by:
- Size
- Weight
- Item value
- Shipping distance
- Chosen carrier
To deliver home and office goods rapidly and in one piece, furniture moving companies follow a few go-to tips:
- Package goods properly with boxes, blankets, bubble wrap, crating, and padding.
- Keep cargo in place with straps.
- Hire a carrier with expertise in furniture moving.
- Book shared truckload (STL) service over the less-than truckload (LTL) and truckload (TL) freight modes.
All of these tips are crucial for affordable, safe, and fast delivery. Furniture movers should give extra thought to the last tip, though, since shipping mode directly impacts service level, satisfaction, and customer reviews. The next step for furniture moving companies? Understanding the differences between furniture shipping services: STL, LTL, and TL.[sc name="anchtag" id="second" ]
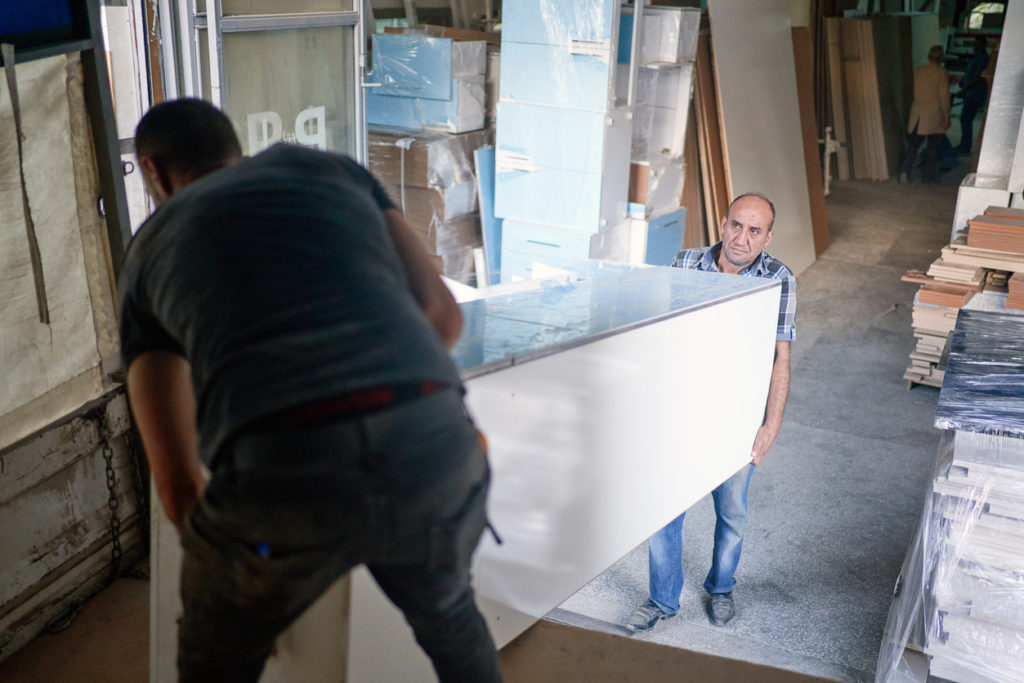
The cons of LTL and TL for furniture shipping
Two standard ways furniture shippers move products are LTL and TL shipping. Both have drawbacks.
LTL: so much work for so little benefit
The LTL mode isn’t ideal for long-distance furniture delivery service due to hub-and-spoke hassles. Here are the issues:
- The struggle to calculate cubic capacity and density (CCD).
- Fees.
- The struggle to understand freight classification.
- The difficulty of accommodating floor-loaded freight.
- Damage.
- Delays.
- Limited tracking visibility.
- High greenhouse gas emissions.
For starters, furniture doesn’t usually fit on the 48”x40” pallets LTL carriers use. As a result, moving companies in the LTL category require super-precise measurements from furniture shippers. This asks a lot of shippers that can’t be 100% sure about CCD. (For accurate CCD dimensions, shippers must tape-measure and weigh each pallet, then enter that information into a density calculator.) Shippers that provide incorrect CCD measurements for six or more pallets — depending on weight — risk incurring fees that can bleed into thousands of dollars.To complicate matters, LTL carriers have varying CCD requirements, making it nearly impossible for shippers with light and large items to assess potential violations.Then there’s the question of freight class. While the freight class of assembled furnishings might be 250, that of disassembled ones could be 500. Noting the wrong freight class is another fee-worthy mistake that shippers can make.Bulky furniture poses another challenge for the hub-and-spoke system: floor-loading. Some furnishings can ship on pallets, but others travel floor-loaded. While truck drivers and dock workers can use automated equipment for palletized freight, they must move floor-loaded shipments by hand. Plus, floor-loaded freight comes loose unless packers fasten it to the deck with tension straps or nails. As a result, LTL carriers typically charge extra for floor-loaded freight or don’t service it at all.Furniture shipments that require special attention throw a wrench in the LTL system, which relies on extensive handling to maximize efficiency. As a result, furniture shipments risk damage and loss as they zigzag through hub-and-spoke facilities.When furniture shippers have to remake single pieces due to damage or loss, customers receive freight late. LTL’s unpredictable transit times can also cause late delivery. Situations of late delivery might be easier to accept if carriers sent a ton of real-time tracking updates. Not so with LTL. Because LTL furniture shipments move between multiple terminals and trucks, tracking visibility is poor. All of this to say: Not only can LTL shippers NOT depend on their freight to arrive intact, on time, or at all, they may never know the status of compromised shipments.Lastly, LTL’s annual greenhouse gas emissions are through the roof: 65 million tons of carbon dioxide equivalent (CO2e). These emissions come from:
- Trucks that drive inefficient routes.
- Carbon-intensive hubs and terminals.
- Repeated resource consumption for replacement goods.
- Energy that powers forklifts and other trans-loading equipment at LTL facilities.
Ultimately, fees, damage, loss, and slow, inefficient transit prevent LTL furniture movers from delivering oversized or heavy items with cost efficiency, ease, and sustainability.Shared truckload solves all of these problems. Before diving into shared truckload, though, furniture shippers should understand their other option: TL.
TL: so much space, so much waste
The downsides of TL moving services are:
- Cost (the most expensive freight mode).
- No load optimization.
- Higher greenhouse gas emissions than any other freight mode.
With TL service, furniture shipping companies pay for a whole truck that moves whether trailers are empty or full. Even though TL service incentivizes shippers to fill trucks to capacity, trailers move with empty space all too often.Because TL service lacks load optimization, several trucks end up doing the job of one, which leads to waste totaling 353-367 million tons of CO2e emissions every year.Shippers can prevent this waste of deck space, money, and fuel by booking shared truckload, which provides the TL service they’re used to at a lower cost.[sc name="anchtag" id="third" ]
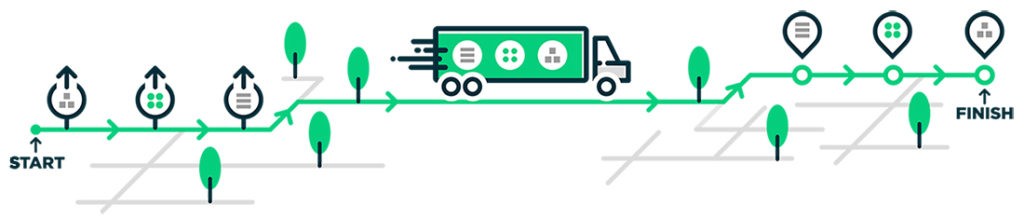
Shared truckload has furniture shippers covered
Furniture shippers that are ready to stop overpaying for trucks they don’t need and sending freight through the damage-prone LTL system can turn to shared truckload, which applies the concept of carpooling to shipping.Shared truckload enables several shippers to split trailer space in one multi-stop full truckload. With shared truckload, shipments that are traveling on a similar route move on the same truck. Shared truckload freight moves directly from its pickup location to its destination — without passing through hubs or terminals. Shared truckload shippers can trust furniture (even floor-loaded pieces) to move without any rearranging during transit. Flock Freight offers a shared truckload solution—FlockDirect®—with benefits that include:
- No freight classes or CCD rules: To send furniture items in a shared truckload, Flock Freight doesn’t ask for freight class or CCD — just linear feet and weight measurements!
- No sneaky fees: Shared truckload shippers avoid CCD, reweigh, reclass, and missed-appointment fees.
- 99.99% damage-free rate: Shared truckload freight stays on one truck for the duration of transit (without handling between destinations), which reduces damage by 120 times.
- Speed: For efficient transit, shared truckloads travel on optimized routes and move directly from freight pickup locations to destinations.
- Control over pickup and delivery dates: When furniture shippers book FlockDirect, they choose their freight’s pickup and delivery dates.
- Sophisticated tracking visibility: Because freight travels on one truck, tracking is a breeze. Flock Freight can tell shippers where their freight is at any given time.
- Straightforward pricing: No pallets? No problem. Flock Freight doesn’t charge different rates based on floor-loaded or palletized freight. Plus, shippers pay for no more space than they need.
- Zero program adjustments: Flock Freight is a standard carrier, which means shippers can keep their existing logistics programs.
- Reduced carbon emissions: Freight moving via shared truckload cuts emissions by up to 40% per shipment, and Flock’s algorithm allows freight to pool at scale.
By providing TL-style service at a lower price point, shared truckload makes furniture shipping cost-effective and reliable.[Learn more about furniture shipping with FlockDirect here.] Read on to learn how ergonomic workstation shipper Grand Stands leverages shared truckload.[sc name="anchtag" id="fourth" ]
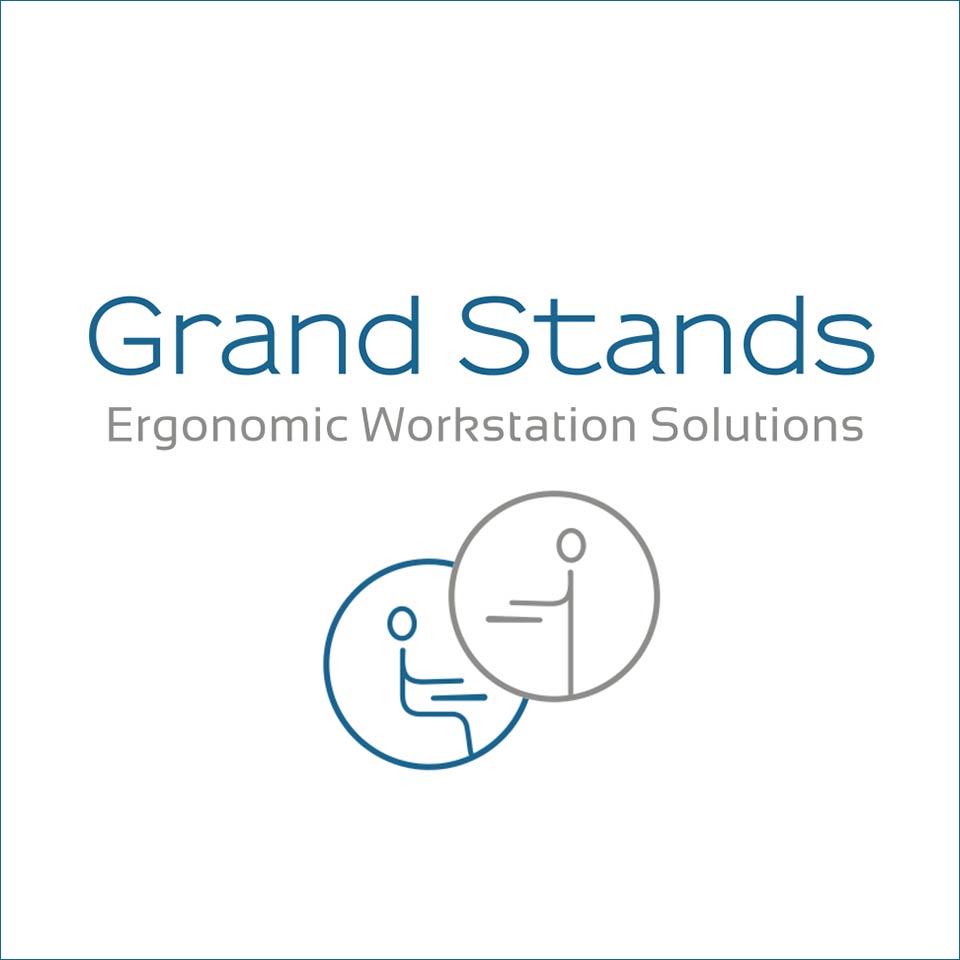
How FlockDirect keeps 100% of Grand Stands’ freight intact
Furniture shipper Grand Stands is a Flock Freight customer that operates from Monrovia, California. The company has been in business for 30 years (since 1991!) and has worked with Flock Freight since 2019.After hearing about Flock Freight through the web, Manuela Brennan, President of Grand Stands, says her team became interested in FlockDirect after learning shared truckload shipments don’t load or unload at hubs. “FlockDirect’s low risk of damage is what led us to Flock Freight,” Manuela recalls.“Now, we book FlockDirect about every other week. We’ve had zero freight damage with FlockDirect,” she shares.Louisville, Kentucky to Monrovia, California is Grand Stands’ most common lane of FlockDirect shipments.Some of the outcomes Grand Stands has seen since the beginning of its partnership with Flock Freight include:
- 94% on-time pickup rate.
- 42,200 total emissions saved.
Here’s how Grand Stands’ FlockDirect shipments performed in first quarter 2021:
- 100% damage-free rate.
- 100% on-time delivery rate.
- 100% on-time pickup rate (February and March).
- 100% reduced emissions.
Flock Freight is here to help furniture shippers like Grand Stands deliver freight safely with excellent performance.[See how other Flock Freight customers benefit from FlockDirect here.][sc name="anchtag" id="fifth" ]
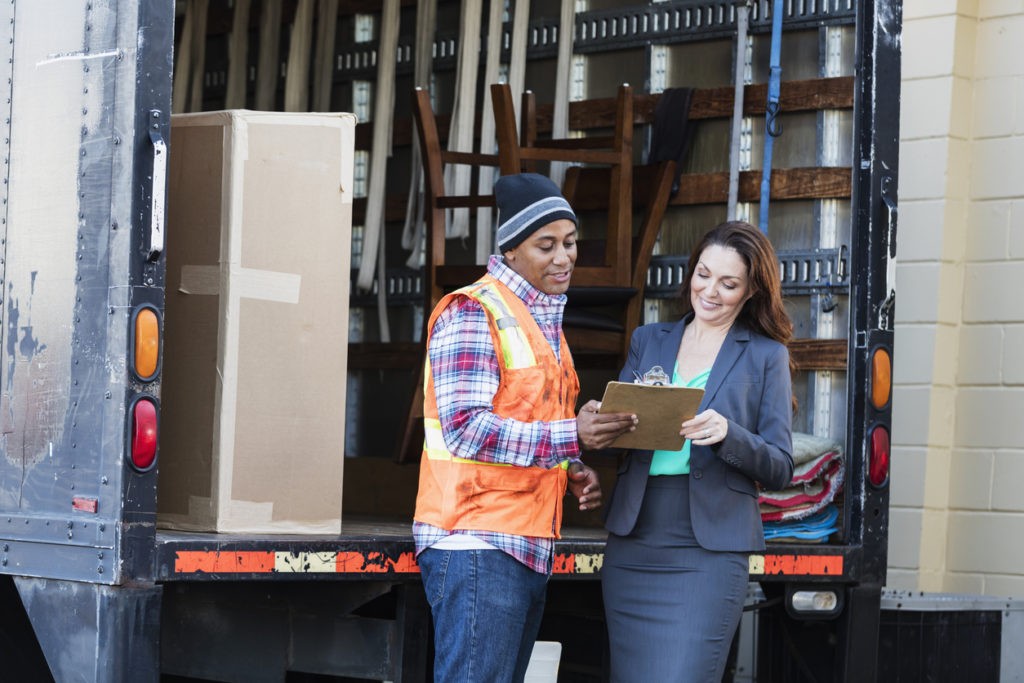
Out with the old, in with the new
While the traditional LTL and TL freight modes make furniture shipping confusing, costly, and slow, FlockDirect is an innovative option that gives shippers what they need: easy, affordable, and quick service.Next time furniture shippers find themselves choosing between the hub-and-spoke system and TL service, they should remember their third option: shared truckload.