How To Minimize Issues in Logistics
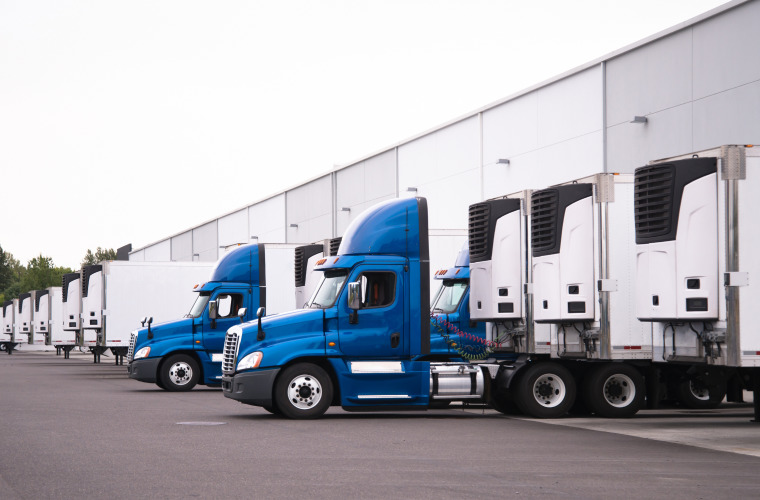
Minimizing freight logistics issues is relevant to businesses now more than ever due to economic stressors and rising customer expectations. For shippers, moving freight as fast as possible and exceeding customer demand have always been key to maintaining competitiveness in their respective industries. But rising costs and supply chain issues can put a damper on your bottom line. While freight logistics is just a part of your entire logistics process, it’s one part that can cause a lot of headaches. This article will examine the most common freight logistics issues and how you can use Flock Freight to negate them.
Most common logistics issues for shippers
While more issues in logistics crop up during natural disasters, economic recessions, and especially the COVID-19 pandemic, there are several common freight logistics challenges that occur year after year.
1. Rising freight costs
Freight costs are a continual thorn in the side for shippers as they fluctuate according to the market. Factors like fuel costs, freight mode, seasonality, and urgency can all impact the cost of your freight. It’s no surprise then that business owners are looking for ways to optimize to become more cost-efficient with their freight shipping. Freight costs that can harm your bottom line include:
- Damage claims
- Late (OTIF) fees
- Market conditions
- Under-utilized trailer space
- Accessorial fees
Freight costs may have seen their peak in 2022, but typical cycles of supply and demand will drive costs back up again. Proactive solutions are needed for most shippers to keep freight costs low and manageable in any market condition. Consolidating shipments, diversifying your freight providers and choosing flexible freight modes can help reduce costs.
2. Delivery delays
A major cause of delivery delays is the hub and spoke model favored by traditional LTL carriers. In this freight transportation model, carriers must travel via a series of centralized distribution centers (hubs) to consolidate less than truckload shipments. This process of multiple stops, unloading, and reloading inherently adds more time to freight transport and can delay delivery to your customers. Additionally, indirect routes and crowded interstates can also contribute to delivery delays. Common freight logistics issues that result in delivery delays:
- Unoptimized routes along the hub and spoke model
- Time spent waiting, unloading, and reloading freight at terminals
- Local traffic and wait times at borders
- Unplanned repair and maintenance schedules of trucks and freight transportation vehicles
- Damaged or lost freight
3. Meeting consumer demand
Many customers now expect fast shipping—and free shipping whenever possible. Faster freight shipping has gradually become the expected norm due to the so-called “Amazon effect” that conditioned customers to expect a level of speed and efficiency far beyond that of traditional freight shipping expectations. These issues in logistics become more substantial when carrier shortages occur. You may be falling behind on meeting customer demand if you:
- Lack visibility/tracking on freight
- Ship freight via slow, inefficient routes
- Deliver damaged freight
- Fail to communicate realistic expectations to customers (or fail to set expectations at all)
4. Reliable carrier partners
Finding reliable carrier partners is key to success in freight logistics, but you may struggle to find and maintain productive relationships with carriers. Often relationships can become strained due to misaligned expectations, lack of clarity and communication between partners, and lack of mutually agreed-upon standards that put the customer first.Many shippers outsource freight logistics to freight brokers, forwarders, or 3PLs to connect their shipments more easily to reliable carriers. However, choosing an unreliable third party can result in the same lack of communication and misaligned expectations.
5. Keeping up with latest technology
Implementing the latest logistics technology can be something of a hit-or-miss operation. In fact, this is often one of the logistics issues holding many organizations back from sustained growth. Companies may fail to adapt or explore new innovations due to fear of higher costs, reluctance to switch platforms, or a healthy skepticism of the “latest and greatest” tech.However, technology in freight logistics is evolving rapidly, and it’s possible that your existing challenges could be minimized by exploring unfamiliar solutions. Each organization should closely monitor logistics tools currently in use and keep an ear to the ground for solutions that address recurring supply chain issues.
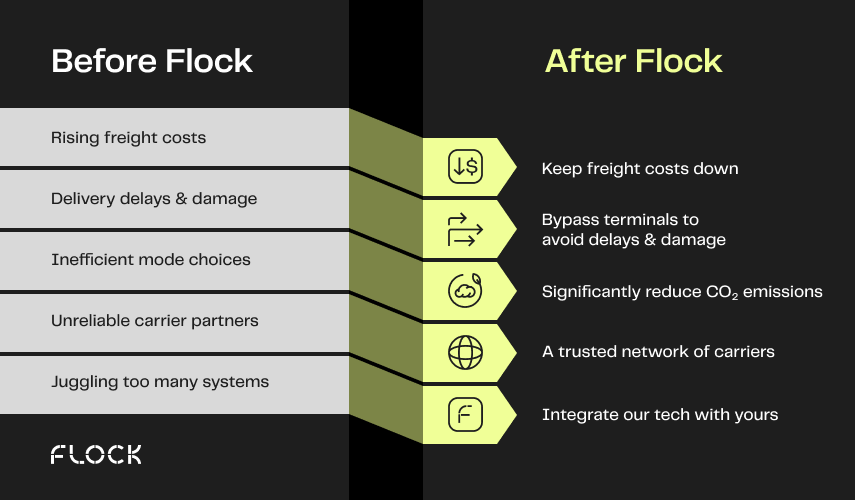
How Flock Freight helps you minimize logistics issues
Freight logistics issues don’t have to put a halt on your business growth. With Flock Freight, you can drive up profit while driving down effort.
1. Keep freight costs down
Rather than contracting the same freight mode for every shipment regardless of size, Flock Freight enables you to pick the right mode for your load—such as full truckload, less-than-truckload, or shared truckload—so that you consistently get the best rates. Additionally, Flock Freight is the only provider in the industry offering shared truckload shipping, which saves you money by pooling your freight on hubless routes that guarantee less damage, lower fees, and more predictable deliveries.
2. Eliminate delays at terminals
If you are shipping less than a truckload via traditional LTL carriers, your freight takes an indirect route where every hub, spoke, and terminal consolidation point increases the chances of delay. Flock Freight offers shared truckload as a smarter alternative to move goods more reliably and with 30% more on-time deliveries than LTL. Eliminate the delays of LTL shipping and get your freight to its destination as fast as possible.
3. Reduce damage and loss
In addition to fewer delays and increased on-time deliveries, terminal-free shared truckload also ships 99.8% damage-free. Your freight stays on one truck, driven by one driver, from origin to destination. Eliminating transloading helps you avoid the high risk of damage common with traditional LTL shipping. This reduces the need for reverse logistics and improves customer satisfaction.
4. Choose carriers from a trusted network
Flock gives you the option to decide which carriers you do (or don't) want to work with. Every driver is vetted and must hold high safety ratings, sufficient insurance, and a positive track record. Flock Freight’s patented technology connects shippers and carriers based on location, schedules, and compatible shipments.
5. Integrate our tech with yours
With Flock’s easy-to-use self-service platform, you can request a quote in minutes to meet your specific requirements. The Flock platform conveniently works with your existing transportation management system (TMS) and freight management processes. You can instantly connect and tender at scale using API and EDI TMS integration technology instead of waiting to connect with a representative.
The takeaway
Despite the challenges in freight logistics, there is hope for businesses looking to capture the benefits of a smarter supply chain such as reduced costs and satisfied customers. With Flock, your organization will be able to sidestep many common freight logistics issues.