How Long Does Freight Shipping Take on Average?
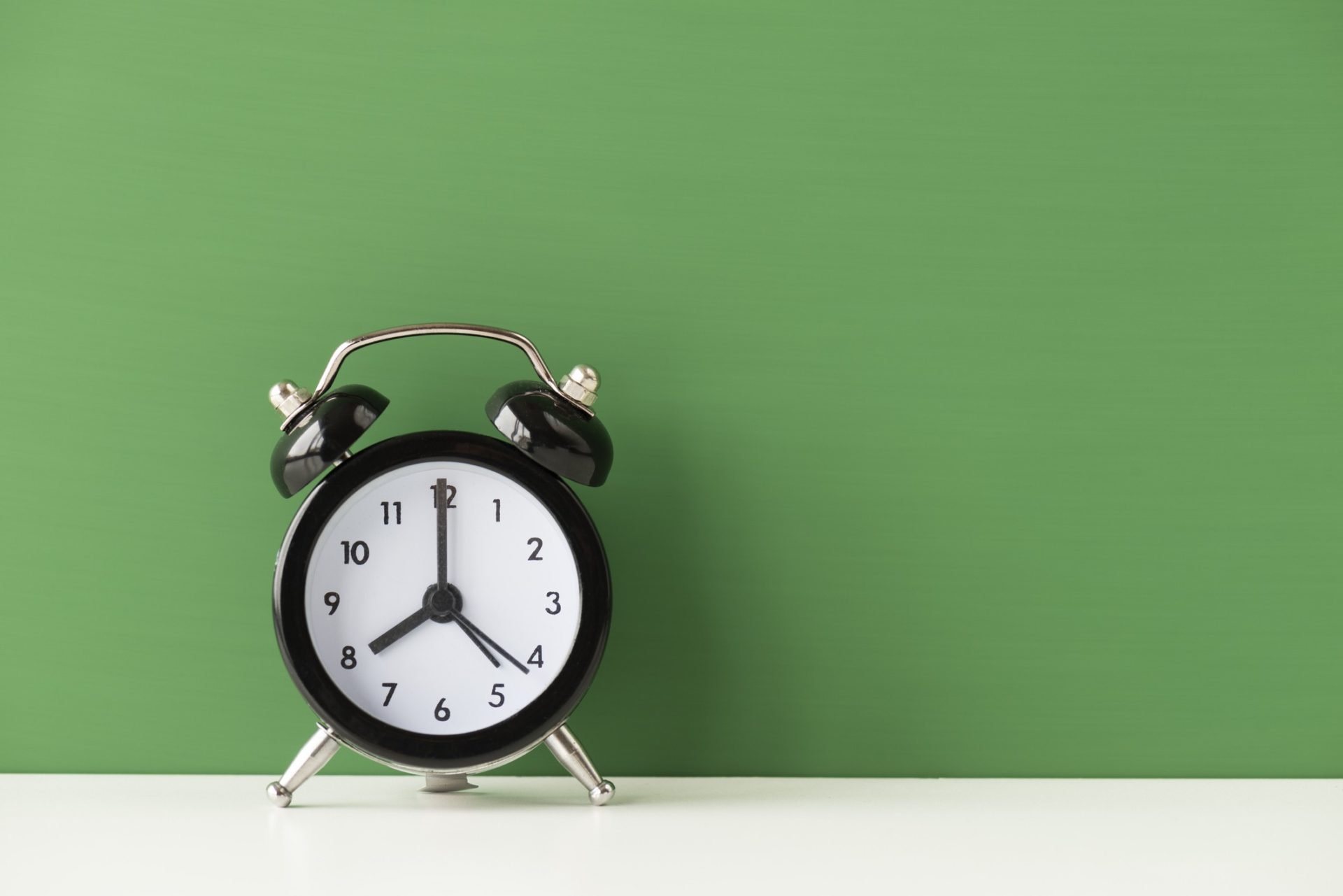
If you’re a business owner who ships regularly, you know how important it is for your customers to receive their shipments in a timely fashion. Changes in the transportation industry over the past few decades have created the expectation in consumers that their goods will be delivered quickly. Failure to do so puts your company’s reputation at risk and threatens your bottom line.
Even if you’re not a business owner, it’s important to know what to expect when you either request a delivery or need to ship items. The delivery process is not the same across the board. There are a variety of factors that can affect the way your shipment is handled and the speed at which it is delivered. Being aware of these variables will allow you to plan your shipments better, see anticipated delivery dates, and avoid any unwelcome surprises during the process.
Shipping Zones
Shipping zones are perhaps the most crucial element to understanding how freight transit times work. Regardless of the contents of a given truckload, shipping zones are the means through which the distance between the departure point and the landing point are estimated. Shipping zones help carriers determine the price of a given shipment, and are vital to planning the logistics of a shipment.
How Do Shipping Zones Work?
Shipping zones are the way carriers measure the distance from a departure location to a truck’s destination. When people first hear the phrase, they assume that it means a fixed system of zones spread throughout the United States, not all that dissimilar from ZIP or postal codes. This isn’t the case. Shipping zones are subjective, which means they're unique to each shipment.
Zones are categorized from Zone 1 to Zone 8. All freight departs from Zone 1, no matter where it is located within the United States. The number of the zone increases with geographic distance from the departure point. For example, if a truck were to depart from Los Angeles, it would be considered Zone 1, and New York would be considered Zone 8.
How Are Shipping Zones Calculated?
It would be reasonable to expect that shipping zones are calculated in terms of miles accumulated, but they’re not. Instead, zones are calculated by ZIP codes.
The USPS website offers a really handy chart which can help you calculate shipping zones based on your ZIP code and the ZIP code you wish to ship to. When you’re navigating the page, click over to the “Get Zone for ZIP Code Pair” tab, and enter the ZIP code where the freight will depart and another for the destination. This will show you where other zones are in relation to yours, and give you a sense of how carriers are interpreting the distance that your freight shipment has to travel.
How Can Shipping Zones Provide Estimated Delivery?
The primary function of zones is to give both LTL carriers and parties looking to ship freight an understanding of how long it will take their goods to arrive at a given destination. The hope is that the simplicity of the zone system will give people an easy metric for making calculations when trying to time shipments.
Keeping in mind that wherever the shipment departs from will be considered Zone 1, zones that are higher in number will be farther away and will inevitably take longer for the freight to be delivered. For example, if you’re in Zone 1 and you need to ship to somewhere within Zone 1 or 2, it’s reasonable to expect that the freight will get there within a few days. There is very little distance to cover. However, if you were shipping from Zone 1 to somewhere in Zone 7 – a significant distance that would probably require stops, highway changes, etc. – then it’s reasonable to expect that the freight will take a few extra days to arrive.
In the last few decades, the process of shipping has become more efficient. Technology has helped guide trucks to more direct routes, load their cargo quickly, and deliver it in a timely fashion. Customers have come to expect this sort of quick service, and by understanding how shipping zones work, it’s possible to hone expectations even more.
Shipping Seasons
While a sound understanding of shipping zones is the best way to think about the way carriers perceive the distance between a truck’s departure point and its destination, shipping seasons are the best way to understand how your estimated freight time might be affected by the time of year.
In a given year, there are stretches of several weeks or even months that are significantly busier than others. During the holiday season, for example, a business must navigate a huge uptick in orders, and freight shipments are requested much more frequently. The same goes for the start of the school year.
While it may seem like the heightened activity would cause shipments times to decrease, often the opposite happens. During the holiday season many businesses give employees time off, and companies tend to slow down. Noticing these trends made it essential that carriers divide the year into seasons so people can have more precise expectations when it comes to delivery time, and figure out when is the best time to ship freight.
- Season One: Estimated freight transit times are the lowest at this time of the year. It spans from January to March, right on the heels of the incredibly busy holiday season. Many customers have already satisfied their shipping needs, which creates a lull where requesting freight shipping is opportune.
- Season Two: The second shipping season is considerably busier than the first. It spans from April through July, the time when a lot of produce is in season and needs to be delivered to grocers. They take up many of the available freight carriers, and finding a truck can be more difficult.
- Season Three: Perhaps surprising to some people, the third shipping seasons is actually the busiest of the year. It spans from August to October and contains back-to-school season. All across the country, parents are ordering things for their kids for the upcoming school year, and trucks fill up incredibly quickly. During this time, it’s also common for people to pre-emptively shop for the holiday season, which also takes up a lot of room on trucks.
- Season Four: The holiday season. It runs from November to December and is very busy much of the time. However, while the beginning is characterized by high shipping volume, it tends to fade towards the end after people have made their purchases and put in their request for freight delivery. Towards the end of the final month, it becomes easy to find space in a truck.
FTL and LTL Shipping and How They Affect Freight Transit Times
When it comes to freight shipping, the mode of delivery is generally divided into two different categories. The first is called Less Than Truckload (LTL) shipping, and the second is called Full Truckload (FTL) shipping. While they achieve the same goal of getting your shipments delivered across the country, they achieve that goal in very different ways.
If you know the difference between the two, you can make a more informed decision based on relevant factors like the size of your shipment and the time you need it by.
FTL Shipping Transit Times
The name Full Truckload basically describes itself. When you order FTL shipping, you’re paying for an entire truck to be dedicated solely to your shipment. No other pallets will share the space within the truck, and the entire drive will be dedicated entirely to one order. Estimated freight transit times are lower for FTL.
- FTL shipments stay on the same truck from the moment the delivery is picked up to the moment it arrives at its destination. They aren’t transferred or touched beyond those two points, and so the risk of damage to goods is severely decreased.
- Because FTL shipping is wholly committed to a single delivery, it is almost always the best delivery option for customers who want to be assured of fast delivery times.
While FTL shipments are most commonly large orders, it’s entirely at the discretion of the shipper whether they want their shipment to be sent using FTL. Factors in the decision can include the size of the shipment, the delicacy of the shipment (FTL orders are handled less), and how quickly the shipment needs to be delivered.
It’s important to note that FTL shipments, while the superior option in terms of logistics, are more expensive that LTL shipments. Because of the specialty treatment they receive and because they take up room that would be otherwise dedicated to other deliveries, the customer has to pay for the entirety of the truck’s time and space.
LTL Shipping Transit Times
Less Than Truckload shipping is the most common freight delivery option used by customers. LTL service is typically smaller than an FTL shipment and weigh less than 4,000 pounds.
However, because LTL shipments involve a truck carrying multiple loads of unique cargo, there are a few drawbacks that don’t affect FTL shipments, including:
- When it comes to transit times, LTL shipping is often slower than FTL. This is because multiple pieces of cargo must be picked up, which usually must be dropped off to different destinations.
- LTL shipments are handled more frequently, not just during the loading and offloading phase, but also during stops when shipments need to be moved around in order to get another off.
While there are some definite drawbacks, many businesses continue to use LTL shipments because they are almost always cheaper than FTL shipments. If time is not a major factor and if your shipment is rather small, LTL rates will save you money while still getting your delivery to its destination city.
Factors That Affect Both LTL and FTL Freight Times
While FTL shipping is almost always a faster delivery method then LTL shipping, some global factors affect them both. When freight times are estimated, these factors are sometimes difficult to calculate and may wind up causing unexpected delays in delivery speeds.
Weather
Despite massive technological leaps forward in the past few decades, it’s still very difficult to precisely predict how weather will affect a given area. When trucks are sent out for deliveries, they look at the forecast along their route, but can’t anticipate everything perfectly.
Trucks that pass through northern states often have to deal with unexpected snow storms, which can cause massive delays on highways. When inclement weather bears down on the road, driving conditions become much more treacherous, and drivers have to either slow down or, if it’s bad enough, wait it out.
Traffic and Construction
It’s difficult to predict weather, but traffic and construction delays are frequently more unforeseeable. While larger roadworks projects are often on a driver’s radar, it’s much harder to anticipate things like traffic jams or congested areas that require re-routing.
Sometimes, an unexpected collision on the highway can hold up traffic for hours or cause a temporary road closure. In these cases, it can take a very long time for trucks to navigate their way to the other side of the collision. Understanding that events like these aren’t likely but still happen with some regularity will help you prepare for possible delays in your shipment.
Conclusion
Freight transit times can be affected by a variety of factors. If you wish for a means of estimating the transit times of your freight, check out a freight transit time calculator to help you set a reasonable expectation for how long it will take your shipments to arrive.